Donald Maybell III, Portfolio Manager – VirTis
In lyophilization there are many variables to consider when specifying the correct equipment to maximize throughput. One component of a lyophilizer, or freeze dryer, that remains a critical piece is the condenser. Depending on the type of lyophlizer, manifold vs shelf, the condenser can be the most critical factor for throughput. How does a user decide what condenser size, type or orientation makes sense for their application and does it matter? The answer depends on the application but regardless it’s best to understand what the trade-offs are for the different options on the market.
This paper will compare the performance of the two most common condenser styles found on pilot/research freeze dryers, Smooth-Wall & Internal Coil. Depending on the application, there can be advantages to having one condenser type over the other.
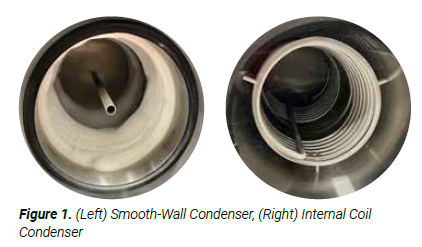
As shown in figure 1, a smooth-wall condenser (left) is designed with the walls of the condenser as the condensing surface. A coil condenser (right) consists of a coil system inside of the condenser chamber as the condensing surface. Condenser performance items to be considered:
- Capacity (both 24 hour load and multi-day total ice)
- Defrost time required
- Clean-ability
- Adequate protection of the Vacuum Pump
- Process scale-up
Condenser Capacity
Condenser capacity is defined by the total amount of ice it is able to condense/collect. This is typically specified over a 24 hour period. In addition, an overall total ice capacity may be specified for when considering multi-day processes. This specification for a lyophilizer is significant to ensure the equipment can hold the total volume of ice condensed from the product/shelves. Keep in mind these specifications are determined with ice, not organic solvents. For comparative purposes, condensers will each have their total ice capacities as specified for the lyophilizer. Smoothwall vs. Internal Coil condenser style provides no substantial difference – condenser capacity is simply a measure of the physical size of the condenser together with the size of its corresponding refrigeration system.
Defrost Time Required
After a recipe has been completed one of the final steps is to defrost the condenser and drain. The amount of ice condensed onto the condenser directly influences the amount of time needed to defrost for coil condensers. Most ice condensers used on research/pilot freeze dryers employ a “hot-gas” defrost approach, whereby heated refrigerant is sent into the condenser coils, causing the coils to warm up and then melt the ice that is in contact with the condensing surface. (Note: larger production freeze dryers would typically use steam or hot water spray for defrost). As some of the ice melts in a coil condenser, the remaining block of ice is still wrapped around the coils, and is not easy to remove. Once there is no contact between the coil and ice, heat transfer slows and further defrost melting can take quite a long
time. The use of any objects to break the ice is not advised as there is risk of damaging the coils. This is not the case for smooth wall condensers. As the ice melts, gravity causes any remaining ice to fall to the bottom of the condenser where it still is in contact with the warmed condenser wall. Significantly less time is needed for defrost. To expedite defrost further, the user could allow the ice to melt enough so the user is able to pull the remaining ice block out of the condenser (figure 2).
For small ice loads of perhaps 1 or 2 liters, the defrost times would be similar. However, for larger ice loads of perhaps 10 or 15 liters, there could be as much as a 6 to 8 hour difference in defrost time.
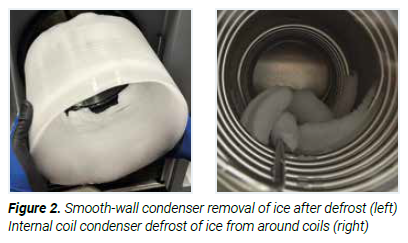
Condenser Surface Clean-ability
Because most research/pilot freeze dryers are not equipped with automatic CIP (Clean-In-Place), condenser cleaning is typically a manual process, such as an IPA wipe-down. Smooth wall condensers are much easier to wipe down and clean after use. Coils condensers are much harder to fully clean as the operators hand can not reach between the coils and the condenser drum. This presents a higher risk of damaging the condenser coils when manually cleaning the system. This may present challenges in a production environment.
Protection of the Vacuum Pump
As shown in figure 3 as ice condenses onto the walls the overall condensing surface area shrinks as more ice condenses onto the walls of the smooth wall condenser (left). The reverse is true for the coil condenser (right), as more ice condenses on the condenser the cooling surface area grows larger until the ice makes contact with the condenser walls then starts shrinking.
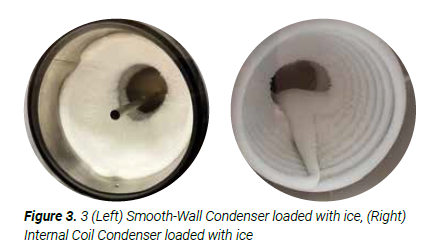
To protect the vacuum pump from vapor bypass going through the condenser into the vacuum pump the system requires adequate condensing capacity. There must be enough interaction of the particles with the condensing surface to remove energy so that the particles condense. If particles are escaping into the vacuum pump then there is risk of damaging the vacuum pump and particles ejecting out the vacuum pump exhaust.
For many applications, condenser type is a less impactful factor to condenser capacity and maximum ice condensing capacity. Due to temperature sensitivity many applications can’t sublimate aggressively enough to overload condensing capacity of either condenser type or load enough volume to overload capacity. In the case where the application can be run aggressively the size of the condenser is a more impactful factor than condenser type. Larger condenser offers larger condensing surface area, condenser capacity and maximum ice condensing capacity.
Scale up
Scale up is a consideration that can be influenced by the type of condenser. Depending on the size of the condenser and the product volumes scale up could be moving to a production sized freeze dryer from a pilot scale or purchasing additional identical units. If the objective is to increase throughput with a larger
system then internal coil condensers somewhat simulate the plate style condensers of production level lyophilizers. Keep in mind when scaling up to a production lyophilizer, even from an internal coil condenser, the environment is completely different so process optimization is still a necessity.
Summary
The unique characteristics of various applications, product volumes and user processes are to be considered when sourcing a lyophilizer. For higher throughput and/or small batch production applications then condenser defrost time and cleanability are the more important factors. In this case the smooth wall condenser design is more optimal for reduced downtime, faster defrost and cleaning. Defrost times are minimized as the user is able to remove ice block once ice is melted away from condenser walls. Cleanability is painless without a coil system hindering accessibility to the walls of the condenser chamber. In the scenario where scalability is favored over defrost time and cleanability then internal coil condenser design is slightly favorable but both condenser designs have been used successfully.