By: SP Genevac
Many solvent evaporators are routinely sited inside fume extraction hoods because residual solvent vapour, remaining in the chamber at the end of a run, can expose the operator to unwelcome, and potentially harmful, odours when the system is opened.
In many cases these situations can be improved significantly by simple changes in programming .
“Odour reduction” adds a repeated vent and vacuum cycle to the end of a method, which purges the evaporation chamber of residual solvent vapours. Utilisation of this function may enable the
evaporator to be sited on the open bench rather than taking up valuable fume hood space.
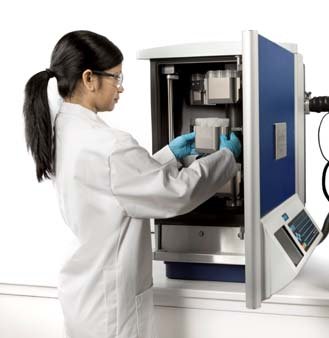
Why does it smell ?
The first thing we need to understand is why a solvent smell is present if the samples are dry and the system has caught all the vapour in the condenser. We’ll explain this by walking through a typical scenario on a Genevac HT systems.
The solvent in this case is pyridine. The smell is overpowering and exposure to it has unpleasant implications.
We finish the drying run at full vacuum and the samples are dry. The run is almost over, and we have pulled as good a vacuum as we can in the chamber. Because any air in the chamber was chased out long ago, and because the system does not leak, the only gas present in the system is pyridine. At ‐45 deg C (condenser temperature) the vapour pressure of pyridine is approx 0.3mbar, so the pressure will not have fallen below that figure.
When the run ends we vent the chamber. We effectively let in 999.7mbar of air, as the total pressure in the chamber is now 1 atmosphere, and we have a mixture of 1 part pyridine to every 3000 parts or air. That is easily enough for a noticeable small when the door/lid is opened.
How else could we have done it ?
When the run is over, instead of ending there, we can add a few more program stages.
First, we vent the system to 50mbar. This dilutes the pyridine 150:1 with air. Importantly, at 50mbar the BP of pyridine only rises to 37 deg C, not high enough to cause condensation on the walls of the chamber.
Then we link to another stage that heads back down to 1 mbar. When we get back down to this pressure, the pyridine will have a boiling point of approximately ‐28 deg C, so the liquid in the trap will stay liquefied. The atmosphere in the chamber is now 1 part pyridine per 150 parts air.
If we then end the run, by letting in another 999mbar of air, the concentration will be pretty much 1 part per 150,000.
If that is not good enough, we can repeat the cycle again. Vent up to 50 mbar (no higher or we might get condensation), pull down to 1 mbar, then end the run and vent fully. This could get the concentration when the door opens down to 1:7,500,000.
Additional vent cycles can be added until the required dilution is achieved.
What about other solvents ?
For each solvent, in order to prevent condensation in the chamber and condenser reflux, the ideal pressure values are different. As a general rule, volatile solvents may be vented up to 100mbar, higher BP solvents may need to be restricted to 20mbar. If you are unsure what settings to use please contact the Genevac applications dept. (applications@genevac.com) for advise on your specific solvent(s).
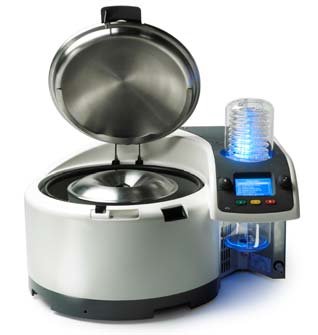
What about other Genevac evaporator systems?
The EZ2 and Rocket evaporators from Genevac both feature an optional “Reduce Odour” function on each method which automatically adds repeated vent and vacuum cycle to the end of a run.
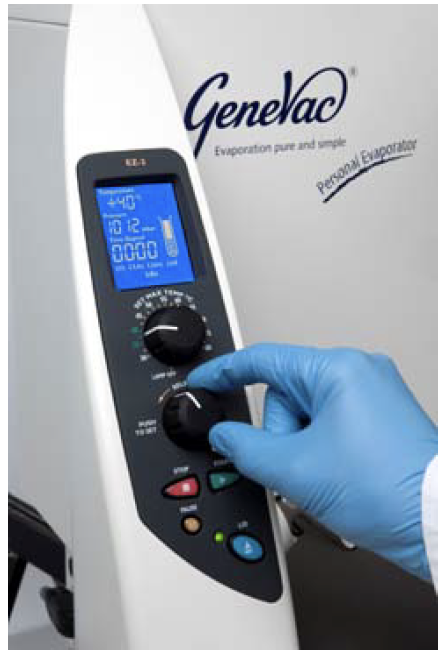
Simply highlight the required method, select Reduce Odour, then chose from the available options: ↑ 100 mbar for low boiling point solvents,↑ 50 mbar or ↑ 20 mbar for higher boiling point solvents (NB. Only setting options appropriate for the selected method are available). Experimentation may be required to find the most effective settings for specific solvents, again please contact the Genevac applications department if you need any advice.