By: Rob Darrington, Product Manager, Genevac Ltd., Stephen Pickrahn, Senior Scientist, International Flavors & Fragrances Inc.
Introduction
In the quest to find novel flavor ingredients from nature, powerful equipment that can produce and concentrate fractions derived from natural extracts is essential. Conventionally, many steps of fractionation and evaluation are necessary until a compound is obtained at the purity required for structural analysis.
International Flavors & Fragrances Inc (IFF) has developed a state of the art fractionation process using the most modern equipment for this purpose. Key components of this system are the Sepbox® instrument made by Sepiatec GmbH (Germany) and the Genevac® HT-24 (Genevac Ltd., UK). The Sepbox allows for two dimensional, preparative scale fractionation of natural products using high performance liquid chromatography – solid phase extraction (HPLC-SPE). In sequential HPLC-SPE / HPLC-SPE steps individual components are isolated from complex mixtures. The Sepbox automates all of these stages.
How it all starts
The increasing demand for “natural” products makes natural product research a potentially lucrative point of research emphasis. The vast variety of plant and animal sources that have been traditionally consumed by mankind makes selecting staring materials crucial for a time and resource efficient approach.
In order to narrow down possible sources for extraction, IFF conducted wide ranging consultation both internally and externally. IFF employs research chefs and flavourists, which were very helpful in directing our sample sourcing. The IFF chefs provided ideas on materials but also prepared several foods as a starting point for extraction. Besides internal recommendations we also researched traditionally used foodstuffs from all around the globe and consulted many other food professionals.
Little is known about the properties a compound must exhibit in order to be taste-active, we believe an exhaustive extraction over a wide range of polar compounds to be the most promising approach. A series of three successive extraction techniques were used, cold and hot organic solvent as well as water are employed. It is quite a challenge for a researcher to look at a flask full of dark, crude “sludge” and liquid as a great deal of work is necessary to isolate just one particular molecule from all of the other materials present. The predicament is that we do not want to loose any potentially successful compounds, but we also don’t want excessive equipment downtime because our samples deteriorate system performance. Several techniques are described in order to remove unwanted components such as chlorophylls and fats [1] which prove useful.
The fractionation process
The design of the Sepbox (figure 1) allows either dry or liquid injection of several grams of sample material. Dry injection is used by IFF. The sample is coated onto a reversed-phase (RP) carrier material. The first fractionation is time-based, using a water-methanol gradient and an ultraviolet (UV) detector. This first separation step yields 16 sub fractions that are trapped onto SPE columns. Each of these initial fractions is further fractionated by a second separation which uses a water-acetonitrile gradient and UV, evaporative light scattering detection (ELSD) detection to monitor the separation. At this point it is an option to trap by time again or by peak, sending the baseline to waste and reducing the number of fractions requiring subsequent workup. In order to streamline our process time-based fractionation is used, giving a constant number of fractions for each sample.
Figure 1: Design of the Sepbox
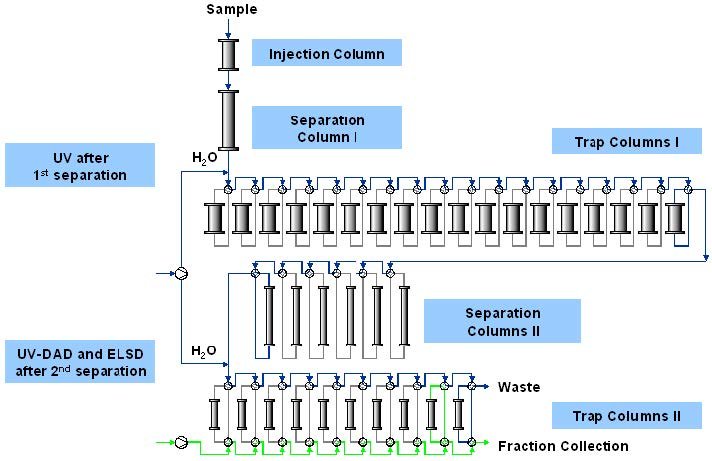
The second trapping is set up to yield 19 sub-subfractions. For trapped polar compounds a different setup is in place which gives 29 fractions. After the first trapping compounds are separated with a wateracetonitrile gradient and directly collected into a fraction collector. A mix of organic solvents is used to elute all the other trapped compounds and collect them in a fraction collector.
The Drying Challenge
Each separation run yields 320 sample vials total, each with a volume of approximately 45ml. The Genevac HT-24 (figure 2) was chosen to dry the samples, because it has two chambers with a large individual vial loading capacity. The vials used to collect the fractions aren’t a standard size, therefore
Genevac designed a custom sample holder to fit. The system can evaporate 192 vials at a time (96 per chamber). Within two days all fractions are dried and ready for further liquid handling and testing. 285 vials contain 45ml of ternary organic solvent mix, with approximately 5% water. Another 35 vials come from a water acetonitrile gradient, from 0 to 100% of each solvent. Conditions for evaporation must be gentle since degradation or even evaporation of possible target compounds would be a great loss. In the
evaporator the evaporation conditions are carefully controlled to provide fast and safe evaporation. The Dri-Pure® system built into the evaporator prevents bumping and cross contamination, and the software in the system controls and monitors the pressures and temperatures of the samples. Temperature measurement is via a thermocouple placed in the sample holder, an additional thermocouple is placed into a sample to provide further feedback on the evaporation process.
Figure 2: Genevac HT-24
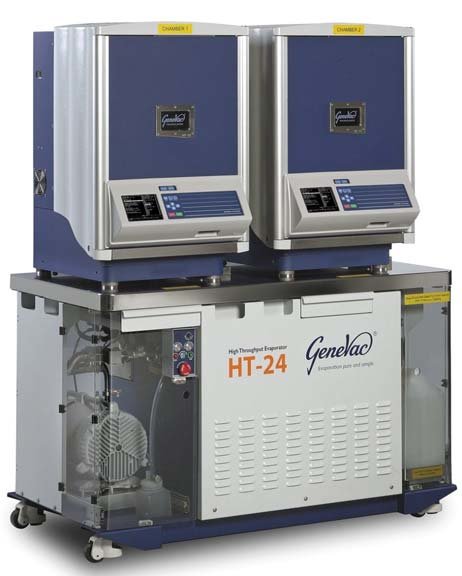
Conclusions
Natural product derived discovery of novel flavor molecules is a highly complex process. Natural product sources yield complex extracts containing many components which may not lend themselves to processing and analysis via traditional laboratory equipment. Based on wide consultation and literature search scientists at IFF have developed a well optimized process to extract, separate, process and evaluate natural product derived sources of flavor molecules.
Every stage of the process must be fully evaluated to ensure that by introducing one element of automation a bottleneck or other problem is not created down stream.
The authors
Stephen Pickrahn is a senior scientist working at International Flavors & Fragrances R&D facility in Union Beach, New Jersey, USA. (Phone: 732-335-2587, e-mail: stephen.pickrahn@iff.com).
Rob Darrington is Product Manager for Genevac, based at their Ipswich, UK head office.
References
[1] Hostettmann et al., Preparative Chromatography Techniques, Springer 1998.
Acknowledgements
Sepbox® is a registered trade mark of Sepiatec GmbH, Berlin, Germany.
Genevac® & Dri-Pure® are registered trade marks of Genevac Ltd, Ipswich, UK.