By: Rob Darrington, Genevac Ltd., Ipswich, UK.
Introduction
Drying high performance liquid chromatography (HPLC) purification fractions, principally comprising water and acetonitrile, is a routine yet essential task in many laboratories. The requirement is to dry the samples to a powder form, such that samples can be accurately weighed, easily sub-sampled and redissolved. Freeze drying is therefore the preferred technology, however, large scale traditional freeze driers may have difficulty processing the organic solvents which can boil out of the samples and damage the vacuum pump. Actelion Pharmaceuticals adopted the fast lyophilisation (LyoSpeed™) methodology developed by Genevac1, and implemented this using the Genevac HT-12 centrifugal evaporation systems. The LyoSpeed method concentrates the organic solvent with the centrifuge controlling boiling preventing sample loss. The system then drains the organic solvent from the condenser and then lyophilises the remaining water. This works well for hydrophilic samples but problems may arise where the sample cannot dissolve in only water – when the organic solvent is removed – the sample then crashes out and/or forms an oil. Such samples require further processing to achieve the desired dry powder form.
Limiting Factors
The success rate (fully lyophilised versus oily compounds) over a standard compound library was averaging approximately 50% with the extremes being as low as 30% or as high as 90%, depending on the compound properties. The simple route to achieving a higher success rate would be to lyophilise the samples with acetonitrile still present in the samples. Unfortunately, this was not possible with the existing equipment.
The limiting factor lies within the hardware, in particular the temperature performance of the solvent condenser (VC3000) of the HT-12 evaporator. The minimum temperature that the VC3000 can achieve is -50°C. This in turn limits the vacuum level that can be achieved in the evaporation system. For good lyophilisation the vacuum should be as low as possible, and ideally below 0.1mbar. For example, at 0.5mbar pure water will boil at -32°C, however, at this low vacuum the boiling point of acetontrile falls to -61°C so it will boil out of the cold trap and choke the vacuum pump, causing the pressure in the evaporation system to rise. As the pressure rises, so does the boiling point of the solvents, leading to poor lyophilisation results, and possibly to complete lyophilisation failure. Whilst the aim of the LyoSpeed methodology is not true lyophilisation, such as may be achieved during production of vaccines, but production of a dry, amorphous powder, rather than an oil. As with true lyophilisation, the better the vacuum, the better the result.
Developing an Superior Solvent Condenser
The solution to the problem seemed clear; a colder condenser was required, one that could condense and hold acetonitrile at a low vacuum. Working with the Engineering team at Genevac, a series of trials was initiated to benchmark the VC3000 against a VirTis Benchtop K -85°C freeze drier (BTK), connected to the HT-12 evaporator.
The results from this lead to the development of an new condenser for the HT-12, called the VC6000 (Figure 1). The design of the VC6000 evolved from the BTK and has been enhanced for higher condensing power, shorter defrosting times, along with the high levels of solvent resistance of a Genevac system.
Figure 1 – Genevac HT-12 with VC6000 condenser
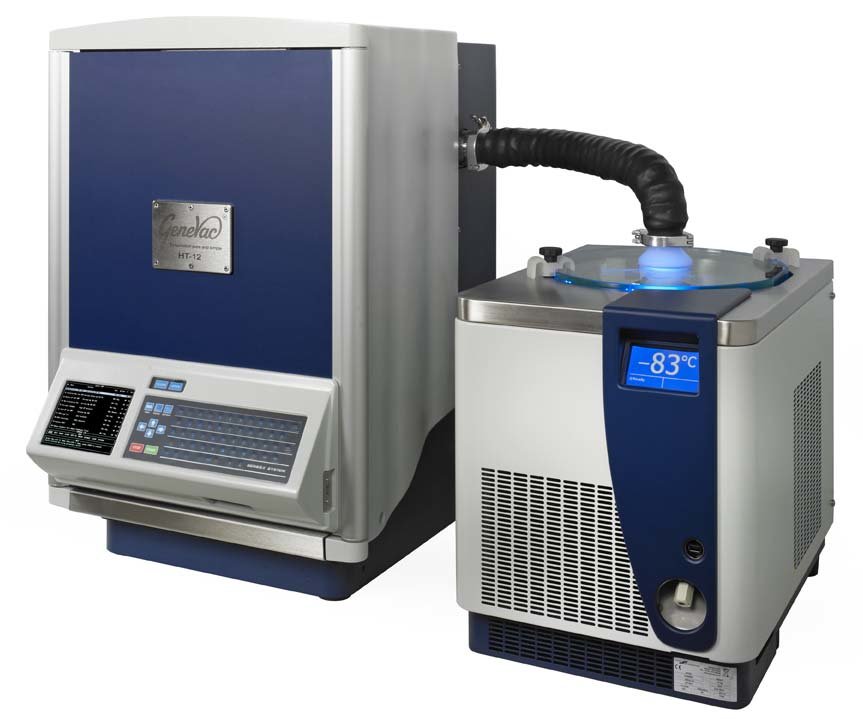
Materials & Methods
The Genevac HT-12 evaporator was used, connected to the VC3000, the BTK, or the VC6000 condenser. Samples comprising 10ml of a 50:50 mix of water and acetonitrile were prepared in 16mm diameter by 100mm tall glass vials, wall thickness 1.2mm. 24 tubes were held in a solid PVDF plastic sample holder and placed in the swing of the HT-12 evaporator. The solvent in each tube contained either: no chemical compound, or, 20mg Diovan, or 20mg of a commercially available, rather lipophilic building block, Phthaloyl-beta-alanine (AI028492). Diovan and AI028482 are both known to be difficult samples to lyophilise from HPLC fractions, and so constitute a “worst case” sample. Each condenser was tested under two load conditions, either with 4 racks of samples – 96 tubes, or a full load of 12 racks – 288 samples.
The method used for all samples and each condenser was the same:
1. Dri-Pure® vacuum ramp over 1 hour to control boiling / bumping
2. Full vacuum with no heat for 3 hours
3. Full vacuum with heat to the sample holders at 40°C for 4 hours
4. Full vacuum with no heat for 18 hours
Stage 4 was excessively long and was used in this way for testing, the actual time to dry can be determined from the chart of logged data.
Results
Following lyophilisation, the condition of the compound in each tube was evaluated as lyophilised successfully to a diffuse powder, or, had formed a light oily sample, or the residual volume of solvent in each tube was estimated. The drying time is taken as the time to temperature convergence of the sample holder and the sample.
Figure 2 – Lyophilisation results for each test condition
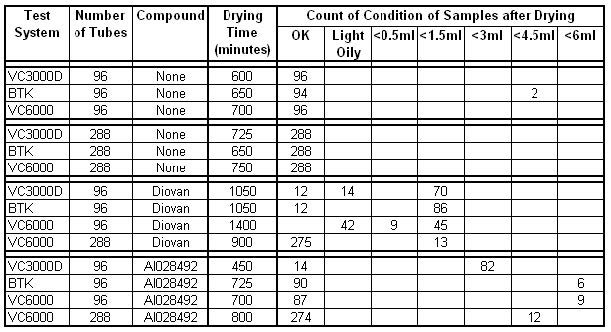
Discussion
Where no sample was present a 100% success rate was expected, it was therefore surprising that 2 of the 96 samples in the BTK did not dry. As this result was not replicated with the higher sample load and was not investigated further – it appears to be an aberrant result.
The performance of the VC3000 when processing real samples was the least successful. The Benchtop K had a better performance but had an inner volume too small for lyophilisation of 288 vials, with the VC6000 performing most successfully, which was in line with expectations. There were two points of interest:
1. Why was the performance of the VC6000 with Diovan so different between the low load and the high sample load? The drying time for the lighter load is also much longer, which is counter intuitive.
2. Given that in each test, the sample in every position is exactly the same, having been drawn from the same stock solution, why is the drying performance so variable between tubes?
The reason for the difference between two Diovan containing tests with the VC6000 is apparent when studying the data plots from the trials, shown in Figure 3a and 3b. In Figure 3a showing the light sample load, the yellow line shows the sample temperature, this never converges with the pink line of the sample holder temperature. This would indicate that samples were still wet, as is born out in the results.
Figure 3a – Data plot from light sample load (96 samples) with Diovan on VC6000
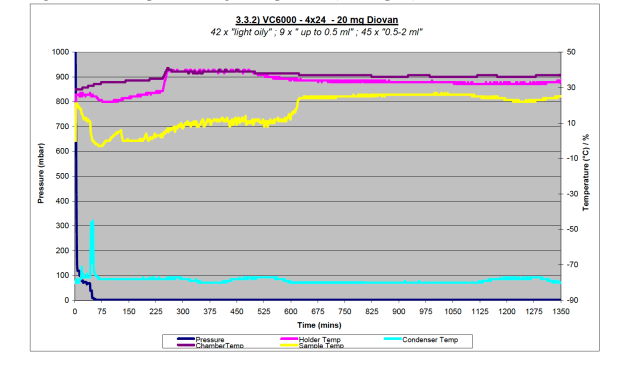
The reason for this was not immediately apparent, and required further investigation. It was found to be inadequate vacuum, approximately 1.5mbar, where samples are less likely to freeze and do not dry well. The ultimate cause of this problem was slight deterioration of vacuum performance of the Scroll vacuum pumps. The choice of Scroll pump is ideal for a system which processes organic solvent vapours, having no oil which may suffer attack. As with any pump, to ensure the optimum performance and gain the best results, regular service is required. In the case of the
Scroll pump routine attention to the tip seals every 3 months maintains performance, is easily done and creates little mess.
Figure 3b – Data plot from high sample load (288 samples) with Diovan on VC6000
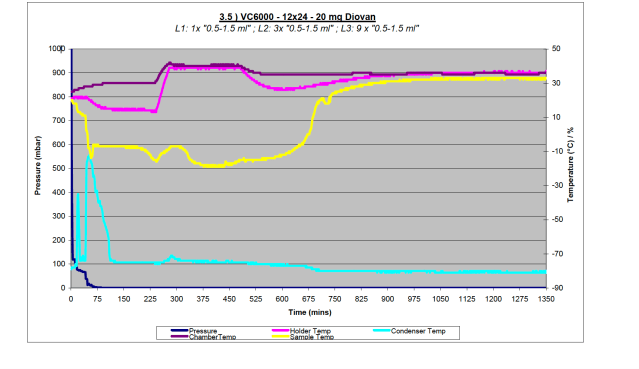
If we study the pressure curves for the three different condensers on processing the same samples, in this case just pure solvent under heavy load, shown in Figure 4, the more powerful and colder condenser (VC6000) is able to keep the pressure low, indicating superior trapping of the solvent. There are two important elements to maintaining the low pressure required for successful freeze drying, good vacuum and a sufficiently cold and powerful condenser.
Figure 4 – Data plot of pressure performance of all 3 Cold traps under high load
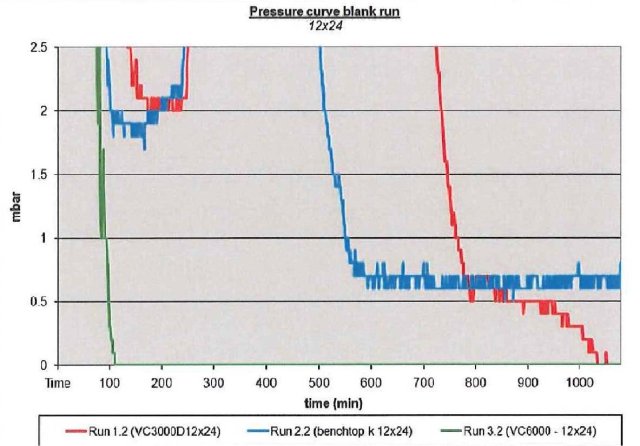
It is difficult to account for the variation in drying performance between tubes in each test. The results for the VC6000 were accurately mapped, one such is shown in Figure 5. As is evident, the tubes that do not dry tend to be those on the edges of the sample holder, however, there are some more centrally located tubes that also do not dry. Figure 5 is typical of all results. One theory which could help account for this pattern is that the centrally located tubes benefit from the cooling effect of the neighbouring tubes, and so freeze and dry more effectively. However, were this the complete explanation, then one would expect to see every peripheral tube fail to dry.
Close observation of the tubes that failed to dry shows no tide line, and suggest that the sample froze, lyophilised and thawed / collapsed – can we conclude that they only sub cooled and evaporated? This is possibly true, however it is not a complete explanation.
Contamination was ruled out as a cause due to scrupulous use of clean new glassware, solvent and samples for every test. An alternative explanation would be due to film formation over the surface of the sample by the compound itself, which would present resistance to, or a total block to evaporation. The concept of “cake resistance” is well described by users of true freeze drying systems, and increases in probability as the depth of sample increases. Results from drying libraries of real research compounds has shown that samples where a film is formed presents a total block to drying, resulting in several millilitres of liquid remaining. Those working with samples report that some libraries with certain chemical properties are prone to form a film. In the case of the trials with AI02492 (Figure 5), it remains unclear as to why a few samples failed to dry. Film formation is one possible cause, however, it cannot be explained why 14 samples failed to dry, whereas 274 dried fully.
Figure 5 – Location of wet tubes following lyophilisation from high load test using AI02492 with VC6000
Key – Yellow = <0.5ml Red = <4.5ml White = dry powder
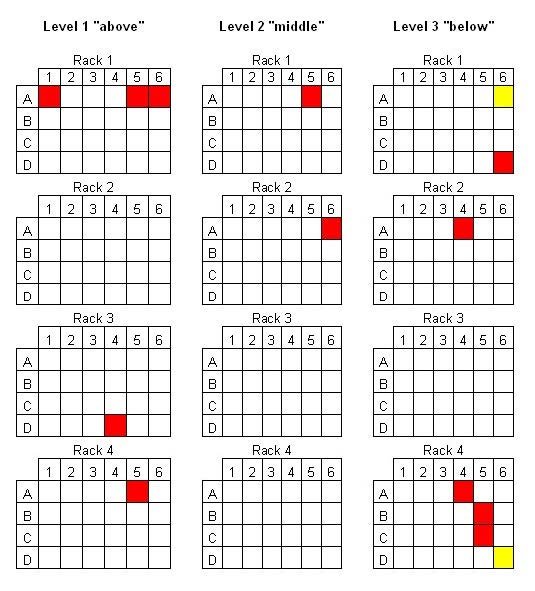
Summary
The tests have shown that the VC6000 delivers superior freeze drying performance, especially under high load, to the other systems tested. Vacuum performance of the system is critical to achieving good results, this requires a vacuum tight system and a sufficiently cold, sufficiently powerful condenser. The VC6000 condensor has been implemented into the daily workflow, and similar evaporation results for “real libraries” of samples containing a wide range of compounds with highly variable solubility patterns (some eluting in 90% organic, and others eluting in 90% water), are routinely observed Some samples are now processed in tubes held in aluminium sample holders, providing identical results.
Acknowledgements
The author gratefully acknowledges Viktor Ribic, Senior Lab Tecnician in the Chemistry Department at Actelion Pharmaceuticals, Allschwil, Switzerland, for his many hours of experimental work, and for providing the results data presented here.
Reference
1. Developments in Laboratory Scale Lyophilisation for Purification Laboratories. Dr Induka Abeysena & Rob Darrington, 2006, available via www.Genevac.com